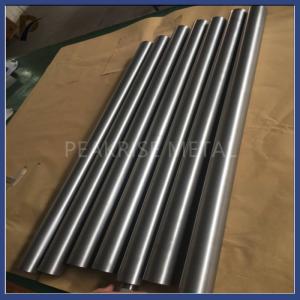
Add to Cart
For use in a molybdenum melting glass electrode, polish molybdenum rod
1. Polished Molybdenum Rod For Molybdenum Melting Glass Electrode Description:
For processing molybdenum electrodes, polishing is a crucial step. The polished molybdenum electrodes have a gray metallic shine and a flat surface. Cutting a metal part's surface with an abrasive-coated, specialized grinding wheel is the process of polishing. In order to improve the flatness and electroplating quality of the parts, polishing can be used to remove a variety of macro defects from their surfaces, including burrs, rust, scratches, weld flashes, welds, sand holes, and oxide skin. All metal materials and some non-metallic materials can be processed using polishing. It can be polished once or numerous times simultaneously depending on the pieces' surface condition and quality requirements. After polishing, parts' surfaces can have a Ra value of 0.4 microns, and oil grinding produces better outcomes. The rigidity and toughness of the polishing wheel, its properties, the quality of the abrasive, and the speed of the wheel shaft's revolution all play a role in the polishing effect.
2. Effect of Glass Quality of Molybdenum Melting Electrode:
One of the key elements determining the quality of the glass is the chroma and transparency of the glass, which are influenced by the molybdenum electrode's quality. The impurity content ratio, density, and homogeneity of the electrode should therefore be tightly controlled during the molybdenum electrode preparation process. When the iron content in molybdenum electrodes surpasses 150PPM, iron, nickel, cobalt, and other metals or metal compounds are the principal causes of glass coloration. There will be a visible green sensation on the glass surface. The green glass will be made after 48 hours of maintaining the temperature. Nickel and iron impurities can also shorten the useful life of molybdenum electrodes.The usable life of molybdenum electrodes can potentially be shortened by nickel and iron impurities. Since their melting points are substantially lower than those of molybdenum and glass, nickel and iron are primarily found in electrodes as single or multiple solid solutions of metal complexes. Since these impurities will melt into the molten glass at high temperatures, the glass will overheat the molybdenum electrode. Early corrosion degrades the glass's quality and lowers the electrode's effectiveness.
The density of the molybdenum electrode is the primary cause of the creation of micro-bubbles in the glass and will also have a slight impact on the quality of the glass and the electrode's lifespan. Continuous precision forging is needed to produce high-density molybdenum electrodes; rotating is not necessary to ensure the surface is straight. The radial distribution is primarily meant by the term "density distribution." The density of the electrode's center is often lower than that of its surroundings, and the difference should be less than 2 to 5 percent. A significant number of micro-molybdenum particles will be integrated into the glass as a result of an excessive difference eroding the molybdenum electrode, which will lower the glass's quality.
3.Actual chemical examination of molten glass electrode with molybdenum:
Element | Ni | Mg | Fe | Pb | Al | Bi | Si | Ca | P | Cu | ||||||||||||||||||||||||||||||||||||||||||||||||||
Concentration(%) | 0.0006 | 0.0006 | 0.001 | 0.0006 | 0.003 | 0.0006 | 0.003 | 0.0006 | 0.001 | 0.0006 | ||||||||||||||||||||||||||||||||||||||||||||||||||
Element | C | O | Sb | |||||||||||||||||||||||||||||||||||||||||||||||||||||||||
Concentration(%) | 0.001 | 0.005 | 0.0006 | |||||||||||||||||||||||||||||||||||||||||||||||||||||||||
Purity(Metallic Base) Mo≥99.95% | ||||||||||||||||||||||||||||||||||||||||||||||||||||||||||||
|
We can process as per customer's drawing and request.
Do you want to know more about our products?